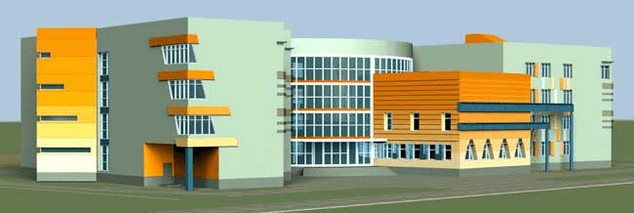
Oszczędność energii w przedsiębiorstwie – główne kierunki:
- Oszczędzanie energii elektrycznej
- Redukcja strat ciepła i pary
- Redukcja strat w przewodach parowych
Oszczędność energii w przedsiębiorstwie - metody oszczędzania energii
- Wybór optymalnej kategorii cenowej i zmiana warunków umownych zasilania
- Optymalizacja silników elektrycznych
- Instalacja VFD
- Optymalizacja systemów sprężonego powietrza
Wybór optymalnej kategorii cenowej dla zasilacza
W sumie istnieje 6 kategorii cenowych zasilania, według których przedsiębiorstwa mogą kupować energię elektryczną od gwarantowanych dostawców.
Wszystkie małe przedsiębiorstwa o mocy zainstalowanej poniżej 670 kW w momencie zawierania umowy na automatyczne zasilanie należą do pierwszej kategorii cenowej.
Wszystkie przedsiębiorstwa o mocy zainstalowanej powyżej 670 kW automatycznie zaliczają się do trzeciej kategorii cenowej.
Pierwsza i trzecia kategoria cenowa nie zawsze są najbardziej optymalnymi i najtańszymi kategoriami zasilania.
W niektórych przypadkach przejście na inną kategorię cenową może obniżyć koszt energii elektrycznej o 5% -30%.
Temat kategorii cenowych jest dość obszerny, w naszym przeglądzie kategorii cenowych szczegółowo mówimy, jak poprawnie obliczyć i wybrać kategorię cenową zasilacza.
Oprócz kategorii cenowych zalecamy również dokładne przyjrzenie się innym aspektom umowy na dostawę energii:
- poziom napięcia,
- moc,
- taryfa przesyłowa energii elektrycznej.
W naszym przeglądzie możesz dowiedzieć się o tych i innych metodach obniżania kosztów energii.
Oszczędność energii w przedsiębiorstwie - silniki elektryczne
Należy wziąć pod uwagę cały sprzęt, w którym używane są silniki elektryczne:
- lakierki,
- kompresory,
- Fani,
- narzędzia maszynowe,
- linie produkcyjne.
Plan sterowania silnikiem elektrycznym
Plan sterowania silnikiem powinien stać się integralną częścią programu oszczędzania energii zakładu.
Taki plan pomoże wdrożyć system długoterminowej oszczędności energii dla wszystkich silników elektrycznych w przedsiębiorstwie.
Plan sterowania silnikiem zapewni, że awarie i awarie nie wystąpią, a jeśli się pojawią, będą rozwiązywane szybko i skutecznie.
Kroki tworzenia planu kontroli silnika:
- Przeprowadź inwentaryzację wszystkich silników w obiekcie.
- Utwórz listę silników z ich głównymi parametrami, stanem technicznym, żywotnością.
- Opracuj ogólne instrukcje przeprowadzania napraw.
- Opracuj wytyczne dotyczące konserwacji zapobiegawczej, smarowania i inspekcji.
- Utwórz zapas bezpieczeństwa często używanych części zamiennych.
- Utwórz specyfikację zakupu nowych silników.
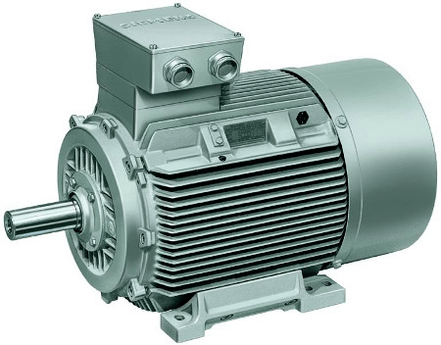
Przezwajanie silników elektrycznych electric
Generalnie przewinięcie starego silnika elektrycznego jest znacznie tańsze niż zakup nowego.
Silnik elektryczny należy wymienić, jeśli koszt przewinięcia przekracza 60% kosztu nowego.
Wtedy wszystko będzie zależeć od tego, jak zostanie przeprowadzone przewijanie.
Jeśli praca zostanie wykonana na najwyższym poziomie, silnik straci tylko 1% -2% procent swojej sprawności.
Jeśli przewijanie zostanie przeprowadzone źle, straty w silniku elektrycznym wzrosną o 5% -10%.
Wymiana starego silnika elektrycznego na nowy energooszczędny ma sens w przypadkach, gdy silnik pracuje ponad 2000 godzin rocznie.
Okres zwrotu nakładów na nowy, energooszczędny silnik nie będzie dłuższy niż 1, 5 - 2 lata.
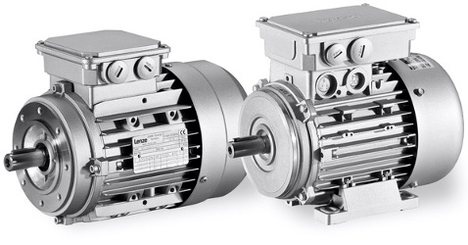
Oszczędność energii w przedsiębiorstwie poprzez zwiększenie współczynnika obciążenia
Współczynnik obciążenia to stosunek mocy roboczej do mocy pozornej.
Tak efektywnie wykorzystuje się energię.
Im wyższy współczynnik obciążenia, tym efektywniej zużywana jest energia elektryczna.
Silnik elektryczny działa optymalnie przy obciążeniu 75% i wyższym.
Dlatego instalowanie silników powyżej wymaganej mocy (ze względów bezpieczeństwa) będzie nie tylko droższe, ale również nieefektywne pod względem zużycia energii.
Współczynnik obciążenia można zwiększyć w następujący sposób:
- wyłączanie nieobciążonych silników,
- wymiana silników obciążonych poniżej 45% na słabsze modele,
- redystrybucja obciążenia pomiędzy istniejącymi silnikami elektrycznymi.
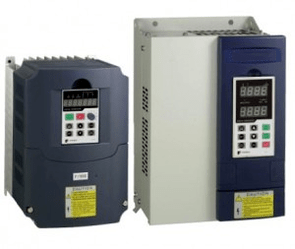
Napęd o zmiennej częstotliwości (VFD)
Instalacja napędów o zmiennej częstotliwości ma sens tylko w przypadku systemów dynamicznych.
W systemach statycznych, które są wykorzystywane na przykład tylko do podnoszenia ładunków, instalacja przemiennika częstotliwości nie pomoże, a często może wyrządzić szkody.
VFD równoważy obciążenie i prędkość silnika, zapewniając w ten sposób optymalne wykorzystanie energii elektrycznej.
VFD może zmniejszyć zużycie energii przez silnik o minimum 5% i maksimum 60%.
Okres zwrotu dla VFD wynosi zwykle 1-3 lata.
Optymalizacja systemów sprężonego powietrza
Sprężone powietrze jest wykorzystywane w wielu gałęziach przemysłu.
W niektórych przedsiębiorstwach głównym konsumentem energii elektrycznej jest sprężone powietrze.
Sprężone powietrze wykorzystywane jest w urządzeniach i urządzeniach pneumatycznych, na przenośnikach, liniach automatycznych.
Stosowanie sprężonego powietrza jest popularne, ponieważ jest wygodnym i bezpiecznym źródłem energii.
Ale wiele osób zapomina, że sprężone powietrze jest jednym z najbardziej nieefektywnych źródeł energii – tylko 5% energii zużywanej na produkcję sprężonego powietrza zamienia się w użyteczną pracę, pozostałe 95% trafia do rury.
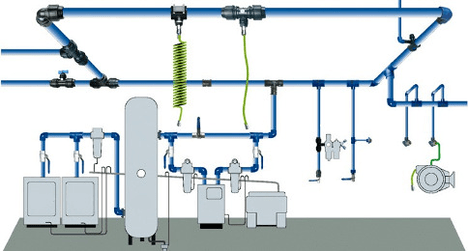
Oszczędność energii w przedsiębiorstwie - sprężone powietrze:
- Nie używaj sprężonego powietrza do czyszczenia pomieszczeń.
- Zmniejszenie temperatury powietrza na wlocie sprężarki o 3% zmniejsza zużycie energii o 1%.
- W przypadku tych procesów technicznych, jeśli to możliwe, zmniejsz ciśnienie sprężonego powietrza do minimum. Obniżenie ciśnienia o 10% zmniejsza zużycie energii o 5%.
- Przeprowadzaj regularne przeglądy, naprawy urządzeń sprężarkowych i linii przesyłowych sprężonego powietrza. Jeden, nawet najmniejszy wyciek sprężonego powietrza, może czasami zmniejszyć wydajność sprzętu.
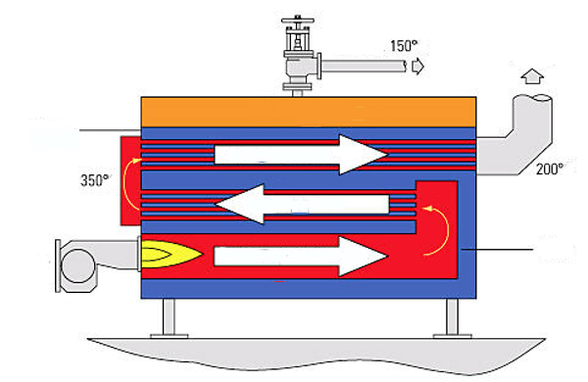
Oszczędność energii w przedsiębiorstwie - ograniczamy straty ciepła i pary
Para jest często wykorzystywana w przemyśle, zwłaszcza w przemyśle tekstylnym, spożywczym i przetwórczym.
Poprawa sprawności kotłów parowych i ponowne wykorzystanie wytwarzanego ciepła może znacznie zmniejszyć zużycie energii w tych zakładach.
Produkcja pary
Kocioł pracuje najwydajniej przy pełnej mocy.
Ze względu na to, że zapotrzebowanie na ilość pary może się zmieniać w czasie, często zdarza się, że kocioł pracuje poniżej swojego optymalnego obciążenia.
Moc zainstalowanego kotła może być znacznie wyższa niż potrzeby przedsiębiorstwa, ze względu na spadek popytu na produkty lub niezrealizowane plany rozszerzenia produkcji.
Również wydajność kotła może nie być wymagana ze względu na ulepszenia procesu produkcyjnego lub wprowadzenie środków oszczędzania energii.
W takich przypadkach kocioł pracuje albo nie z pełną mocą, albo w trybie krótkich cykli włącz-wyłącz.
Obie te sytuacje pociągają za sobą znaczne straty energii.
Nie ma prostych i tanich rozwiązań tego problemu.
Najłatwiejszą opcją jestzainstalować „mały" kocioł, który będzie pracował z pełną mocąprzy średnim lub niskim obciążeniu pracą w przedsiębiorstwie.
Pomimo tego, że nie jest to tanie rozwiązanie, okres zwrotu takiej inwestycji może być krótszy niż dwa lata.
Ogólnie rzecz biorąc, zawsze bardziej wydajne jest posiadanie kilku małych wymiennych kotłów, zwłaszcza w przedsiębiorstwach o zmieniającym się zapotrzebowaniu lub znacznych sezonowych wahaniach zużycia ciepła i pary.
Automatyczny system regulacji
Jeśli przedsiębiorstwo ma kilka kotłów, warto zainstalowaćautomatyczny system regulacji obciążenia kotłów. . .
Automatyzacja odpowiada na zapotrzebowanie na parę w przedsiębiorstwie, redystrybuując obciążenie między kotłami, włącza lub wyłącza kotły, tym samym znacznie zwiększając wydajność całego systemu.
Zasuwa
W przedsiębiorstwach, w których kotły są regularnie wyłączane z powodu spadku zapotrzebowania na parę, straty ciepła przez komin mogą być dość wysokie.
Istnieje możliwość zablokowania utraty gorącego powietrza przez komininstalując zasuwęktóry zamyka rurę, gdy kocioł jest wyłączony.
Zapobieganie i konserwacja
Pozostawione bez nadzoru palniki i systemy odprowadzania skroplin mogą szybko ulec pogorszeniu lub awarii.
Może to obniżyć sprawność kotła o 20% -30%.
Prosty program konserwacyjny – zapewniający, że wszystkie elementy kotła działają na maksymalnym poziomie – znacznie podniesie wydajność operacyjną.
W praktyce regularna konserwacja zmniejsza zużycie energii przez kocioł o 10%.
Izolacja - straty ciepła z powierzchni prawidłowo zaizolowanego kotła powinny wynosić poniżej 1%.
Usuwanie sadzy i kamienia
Konieczne jest ciągłe monitorowanie i eliminowanie powstawania sadzy na rurach kotłowych, kamienia kotłowego.
Warstwa sadzy o grubości 0, 8 milimetra zmniejsza przenoszenie ciepła o 9, 5%, a warstwa o grubości 4, 5 milimetra o 69%!
Kamień tworzy się, gdy wapń, magnezja i krzem osadzają się na wymienniku ciepła kotła.
Skala o grubości 1 milimetra zwiększa zużycie energii o 2%.
Sadzę i kamień można usunąć mechanicznie lub kwasami.
Powstawanie sadzy i kamienia kotłowego można określić na podstawie wzrostu temperatury spalin lub oględzin, gdy kocioł nie pracuje.
Powstawanie sadzy i kamienia kotłowego należy szczególnie uważnie kontrolować, jeśli kocioł pracuje na paliwie stałym (węgiel, torf, drewno opałowe).
Kotły gazowe są mniej podatne na problemy z sadzą.
Optymalizacja odmulania kotła
Odmulanie kotła to odprowadzanie wody kotłowej w celu oczyszczenia wody wewnątrz kotła z zanieczyszczeń i soli.
Celem odsalania kotła jest uniknięcie lub ograniczenie tworzenia się kamienia kotłowego.
Niedostateczne przedmuchanie kotła może prowadzić do przedostawania się wody do pary lub tworzenia się osadów w kotle.
Nadmierne wydmuchiwanie oznacza utratę ciepła, wody i chemikaliów.
Optymalny poziom odsalania zależy od typu kotła, ciśnienia roboczego w kotle, przygotowania i jakości używanej wody.
Pierwszą rzeczą, na którą należy zwrócić uwagę, jest przygotowanie wody. Jeśli woda jest dobrze uzdatniona (niska zawartość soli), stopień wydmuchu może wynosić 4%.
Jeśli w wodzie znajdują się obce substancje i sole, wskaźnik wydmuchu wyniesie 8% -10%.
Automatyczny system odsalania może również znacznie zmniejszyć zużycie energii.
Okres zwrotu takiego systemu wynosi zwykle 1-3 lata.
Redukcja emisji dymu
Nadmierne zadymienie jest często wynikiem wnikania powietrza do kotła i komina przez nieszczelności i otwory.
Zmniejsza to wymianę ciepła i zwiększa obciążenie układu sprężarki.
Nieszczelności i dziury można łatwo wyeliminować, konieczne jest jedynie okresowe przeprowadzanie oględzin kotła i komina.
Regulacja powietrza
Im więcej powietrza zużywa się do spalania paliwa, tym więcej ciepła jest wyrzucane na wiatr.
Ilość powietrza nieco powyżej idealnego stosunku stechiometrycznego paliwo/powietrze jest konieczna ze względów bezpieczeństwa, aby zmniejszyć emisje NOx i zależy od rodzaju paliwa.
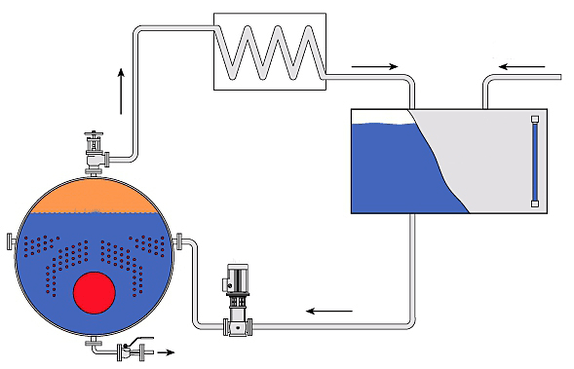
Kotły w złym stanie technicznym mogą zużywać do 140% dodatkowego powietrza, co powoduje nadmierną emisję spalin.
Wydajny palnik gazowy wymaga od 2% do 3% dodatkowego tlenu lub od 10% do 15% dodatkowego powietrza, aby spalić paliwo bez wytwarzania tlenku węgla.
Ogólna zasada jest taka, że sprawność kotła wzrasta o 1% na każde 15% redukcji dodatkowego powietrza.
Dlatego konieczne jest ciągłe sprawdzanie stosunku paliwo / powietrze.
To wydarzenie nic nie kosztuje, ale ma bardzo dobry efekt.
Monitorowanie emisji dymu
Ilość tlenu w spalinach to suma dodatkowego powietrza (dodawanego w celu zwiększenia bezpieczeństwa i redukcji emisji) oraz powietrza, które przedostaje się do kotła przez otwory i nieszczelności.
Obecność nieszczelności i dziur można łatwo wykryć, jeśli zostanie ustanowiony system monitorowania dopływającego powietrza i ilości tlenu w spalinach.
Wykorzystując dane o ilości tlenku węgla i tlenu można zoptymalizować stosunek paliwo/powietrze w kotle.
Instalacja systemu monitorowania i analizy emisji spalin zwykle zwraca się w czasie krótszym niż rok.
Oszczędność energii w przedsiębiorstwie — instalacja ekonomizera
Ciepło ze spalin można wykorzystać do podgrzania wody wpływającej do kotła.
Podgrzana woda dostaje się do kotła i wymaga mniejszej ilości ciepła do przekształcenia w parę, oszczędzając w ten sposób paliwo.
Sprawność kotła wzrasta o 1% na każde 22°C spadek temperatury spalin.
Ekonomizer może zmniejszyć zużycie paliwa o 5% - 10% i zwróci się w niecałe 2 lata.
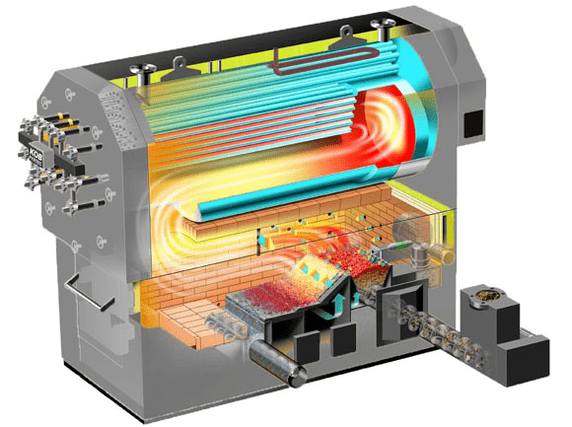
Wymiennik ciepła do pobierania ciepła z wody i pary z odsalania kotła
Wymiennik ciepła pomoże odzyskać około 80% ciepła wody i pary z przedmuchu kotła.
Ciepło to można wykorzystać do ogrzewania budynków lub podgrzewania wody zasilającej kocioł.
Każdy kocioł ze stałą szybkością odsalania 5% lub więcej jest doskonałym kandydatem na wymiennik ciepła.
Jeśli system odsalania nie działa w trybie ciągłym, warto pomyśleć o przeniesieniu go do trybu stałego, jednocześnie instalując wymiennik ciepła.
Średni okres zwrotu dla wymiennika ciepła nie przekroczy 1, 5 - 2 lat.
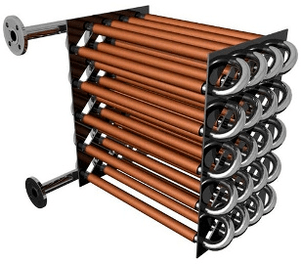
Instalowanie ekonomizera kondensacyjnego
Gorący kondensat można zawrócić do kotła, oszczędzając w ten sposób energię i zmniejszając zapotrzebowanie na uzdatnioną wodę.
Ekonomizer kondensacyjny może zwiększyć wydajność systemu o dodatkowe 10%.
Instalacja takiego ekonomizera powinna odbywać się pod ścisłym nadzorem specjalistów, którzy uwzględnią wszystkie niuanse takiego systemu, jego wpływ na kocioł i skład chemiczny wody.
Korzystanie z systemu, który zwraca kondensat z powrotem do kotła, zwykle zwraca się w ciągu 1-1, 5 roku.
System kierujący kondensat do źródła ciepłej wody zwraca się w niecały rok.
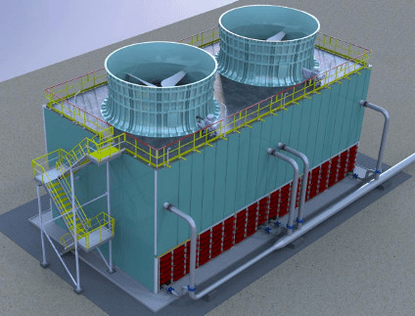
Wieże chłodnicze (wieże chłodnicze)
Chłodnia kominowa to wymiennik ciepła, w którym woda jest chłodzona strumieniem powietrza.
A jeśli chodzi o efektywność energetyczną, wieża chłodnicza to urządzenie, które odprowadza ciepło na wiatr.
Potencjał oszczędności energii w wieżach chłodniczych:
- W niektórych przedsiębiorstwach sensowna jest całkowita rezygnacja z chłodni kominowych. Istnieje wiele przypadków, w których ogrzewanie służy do ogrzewania pomieszczenia, a jednocześnie do rozpraszania ciepła wykorzystywana jest wieża chłodnicza. Zainstalowanie pompy ciepła rozwiąże problem ogrzewania i przynajmniej częściowo zredukuje potrzebę korzystania z chłodni kominowej.
- Zainstalowanie wyłączników automatycznych dla wentylatorów wieży chłodniczej może zmniejszyć zużycie energii o 40%.
- Wymiana wentylatorów aluminiowych lub żelaznych na nowe (z włókna szklanego i tworzywa sztucznego) może zmniejszyć zużycie energii nawet o 30%.
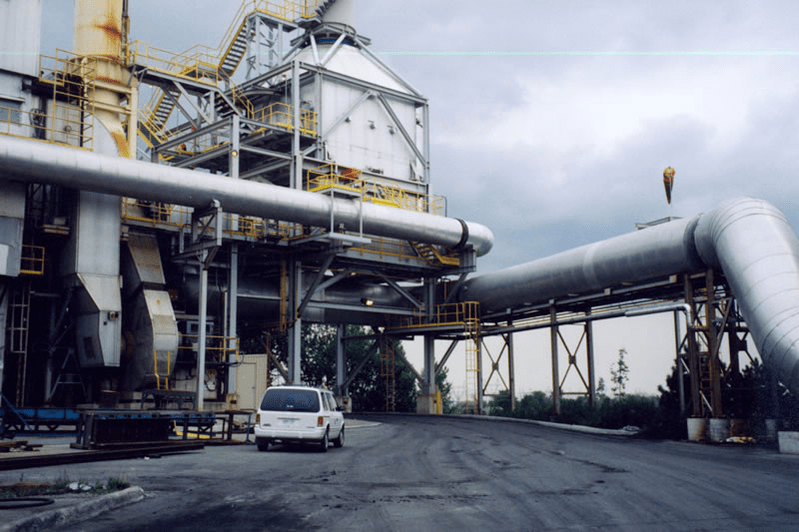
Redukcja strat w przewodach parowych
Odłączanie nieodebranych linii Steam
Potrzeby i zużycie pary ciągle się zmieniają.
Może to prowadzić do tego, że cały system dystrybucji pary nie jest wykorzystywany z pełną wydajnością, a jedynie 20% -50%, co nieuchronnie prowadzi do strat ciepła.
Oczywiste jest, że optymalizacja lub rekonfiguracja całego systemu dystrybucji pary w celu zaspokojenia nowych potrzeb będzie bardzo kosztowna i być może niewykonalna.
Jednak identyfikacja i wyłączanie rzadko używanych przewodów parowych może być bardzo skutecznym środkiem oszczędzania energii.
Oszczędność energii w przedsiębiorstwie - Izolacja termiczna rur
Izolowanie rur parowych może zmniejszyć straty energii nawet o 90%.
Jest to jeden z najszybszych zwrotów oszczędności energii w systemie dystrybucji pary.
Średni okres zwrotu za izolację rurociągów, którymi przesyłana jest para lub gorąca woda, wynosi około 1 roku.
Rury kondensatu przez 1, 5-2 lata.
Monitoring odwadniaczy
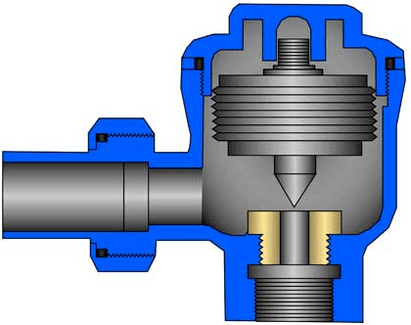
Prosty program monitorujący stan techniczny odwadniaczy może znacznie ograniczyć straty ciepła.
Na przykład, jeśli konserwacja nie była przeprowadzana przez 3 do 5 lat, z reguły około jedna trzecia odwadniaczy jest niesprawna, co pozwala parze przedostać się do systemu odprowadzania kondensatu.
Z praktyki w przedsiębiorstwach, które mają program monitorowania odwadniaczy, nie więcej niż 5% odwadniaczy jest w stanie wadliwym.
Średni okres zwrotu kosztów wymiany lub konserwacji jednego odwadniacza wynosi mniej niż sześć miesięcy.
Program monitorowania odwadniaczy zazwyczaj zmniejsza straty pary o 10%.
Odwadniacze termostatyczne
Zastosowanie nowoczesnych odwadniaczy termostatycznych może zmniejszyć zużycie energii i jednocześnie zwiększyć niezawodność całego systemu.
Główną zaletą odwadniaczy termostatycznych jest to, że:
- otwarte, gdy temperatura zbliża się do poziomu pary nasyconej (+/- 2 C°),
- emitować nieskraplające się gazy po każdym otwarciu i
- znajdują się w stanie otwartym na początku pracy systemu, co zapewnia jego szybkie nagrzewanie.
Ponadto te odwadniacze są bardzo niezawodne i mogą być stosowane w szerokim zakresie ciśnień.
Odłączanie odwadniaczy
Możesz zmniejszyć zużycie energii, wyłączając odwadniacze na przewodach pary przegrzanej, gdy nie są używane.
Eliminacja wycieków pary
Program naprawy wycieków pary z małych otworów może zwrócić się w czasie krótszym niż 3 do 4 miesięcy.
Nie wolno nam zapominać, że małe wycieki mogą pozostać niezauważone przez lata, stale uszkadzając system.
Ponowne wykorzystanie kondensatu i pary
Kiedy odwadniacz odprowadza kondensat z systemu parowego, spadek ciśnienia wytwarza parę z tego kondensatu.
Para ta wraz z kondensatem może być wykorzystana w wymienniku ciepła do podgrzewania wody zasilającej lub powietrza.
Co najważniejsze, możliwe jest wykorzystanie tej pary i kondensatu w pobliżu miejsca uwolnienia, ponieważ stworzenie oddzielnego systemu rurociągów do transportu go do miejsca użycia może być bardzo kosztowne.